Goldenbet in UK
Goldenbet is a non-stop online casino that provides its players with an extensive gaming library of over 6,000 games. The casino offers a variety of casino games including slots, table games, live casino games and more.
Official site | cubeprecision.com |
Year of release | 2021 |
Number of games | 6000+ |
Mobile version | Android, IOS |
Bonus | 100% Bonus up to £ 500 |
Game content | Slot machines, Mini games, live casino games, table games |
Goldenbet also offers attractive promotions, starting with a generous welcome bonus and free spins to keep its players interested. Whether you are an experienced player or a beginner, Goldenbet is a great platform to experience the excitement of online gambling.
Casino Bonuses: A guide to the best promotions and offers 2024
You can find many goldenbet bonuses that the casino offers to its new and regular players. The most popular one is the welcome 100% bonus up to £500. The list of other promotions also includes: 10% cashback bonus, 3 + 1 freebet, 100% welcome bonus on sports, welcome bonus on cyber sports and many more.
W4elcome bonuses are given to newly registered users. But you can find special bonus codes on various affiliate websites to take advantage of some exciting promotions that are only available for a certain time.
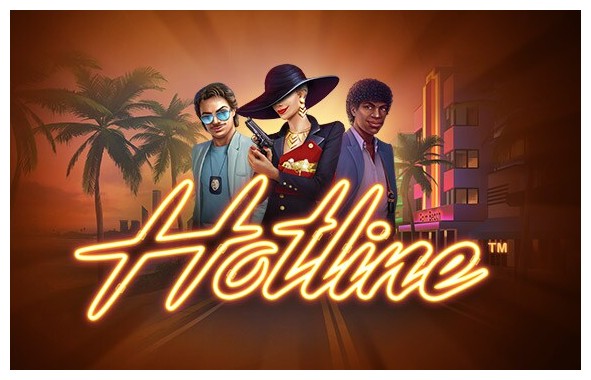
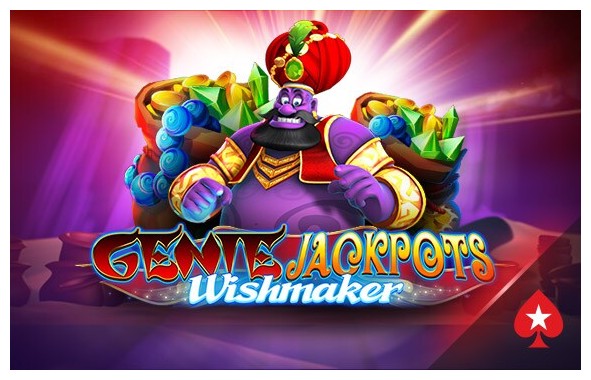
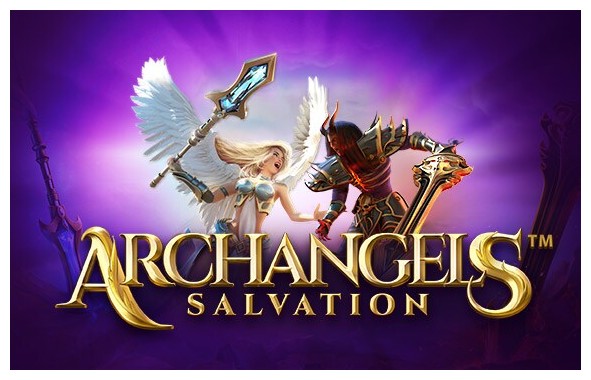
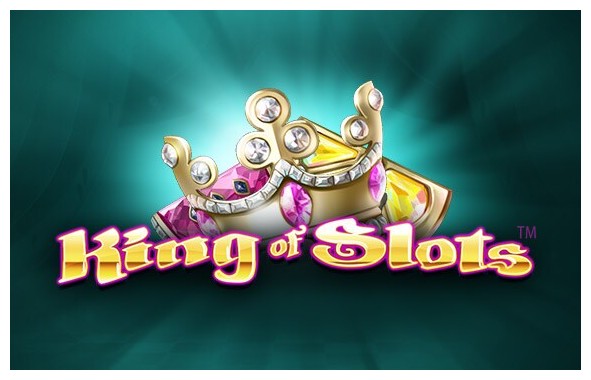
If you are interested in the terms and conditions of the bonuses, you can read them on their website. There are wagering requirements attached to all bonuses, but they are quite low. And so far, players have had no problems fulfilling them.
Casino Games and Providers: Discover the top slots and table games
Golden Bet Casino has over 6,000 slot machines in its library, an astounding number, isn’t it? You can search for your favourite games in the drop-down menu. In addition, you can also customise the section and pin your favourite slots in the ‘My Favourites’ section.
You can also search for slots based on popularity. Goldenbet has plenty of Megaways and jackpot games, as well as a search function for recently added online slots.
The most popular options are some Play’n Go and Netent slot machines such as Starburst XXXTREME, Book of Dead, Legacy of Dead and more. You can also go to the jackpot games section and if you’re lucky, you can get some extra winnings.
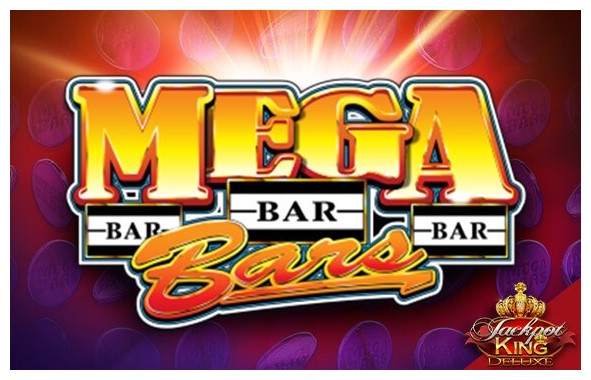
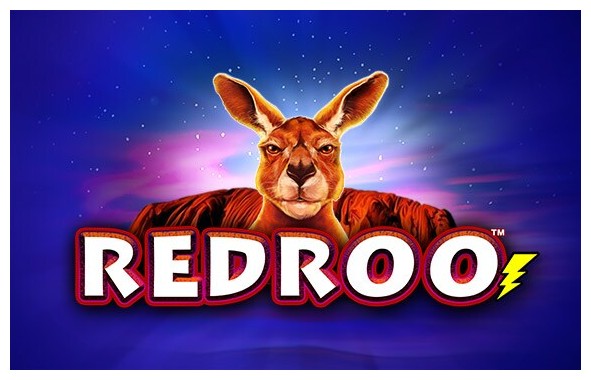
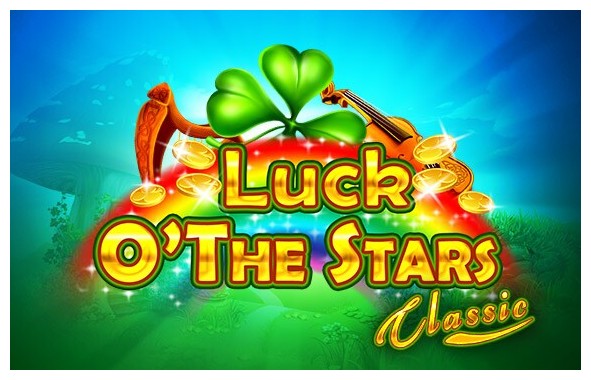
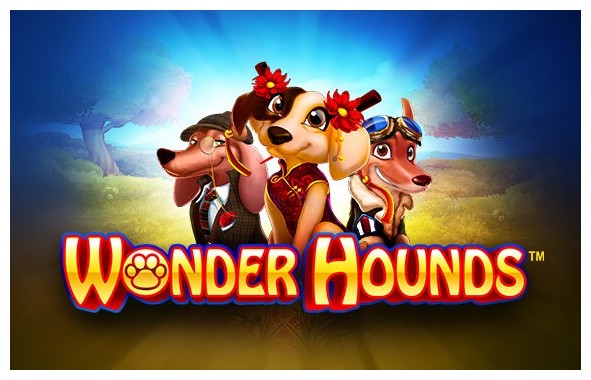
Payments and casino support: All payment methods and 24/7 customer support
Goldenbet offers a variety of payment options. The most convenient ones are displayed in the user’s payments section, taking into account the currency specified during registration in the user’s country. Goldenbet is one of the best credit card casinos. Apart from card payments, in also includes other payment methods such as Sofort, MiFinity, Skrill, Neteller, Bitcoin, Dash, Ripple, Ethereum, Monero, Tether and dozens of other options.
If you need help with Goldenbet, you can get answers here:
- Q&A. Get details on how to contact support and how to sign up here.
- Email. Send an email
- Chat. Instantly send a message to the support team in chat.